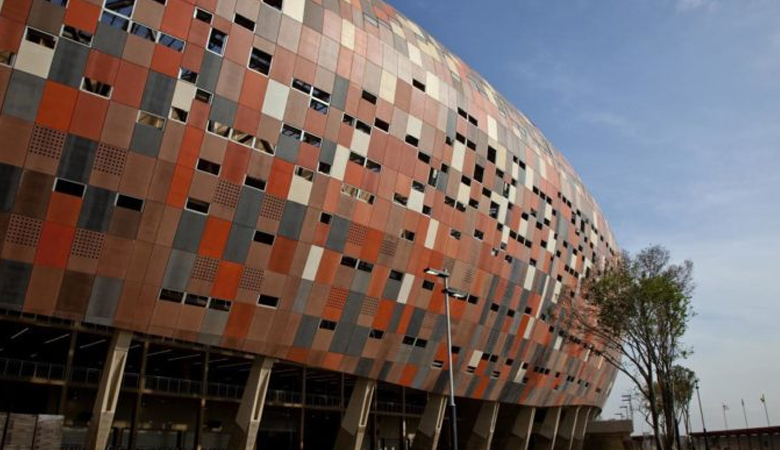
03 abr Concreto GFRC: o que é essa novidade do ramo civil e quais suas grandes vantagens?
O Glass Fiber Reinforced Concrete (GFRC) é um microconcreto composto à base de cimento reforçado com fibras de vidro álcali resistentes. O material proporciona efeitos arquitetônicos de alto e baixo relevo que seriam impossíveis de serem obtidos com outros concretos, possibilitando moldar painéis de fachada exatamente de acordo com o projeto de arquitetura.
O que é GFRC?
GFRC é a sigla para Glass Fiber Reinforced Concrete que, traduzindo para o português, significa Concreto Reforçado com Fibras de Vidro.
Portanto, o GFRC, também conhecido apenas por GRC, é um microconcreto composto à base de cimento reforçado com fibras de vidro álcali resistentes. O material torna possível projetar peças de diversas formas com pequenas espessuras.
As principais características do material estão relacionadas à leveza, elevada resistência e durabilidade. O desenvolvimento do GFRC ocorreu na década de 1960, com o propósito de reforçar compósitos de concreto e cimento.
Nos dias de hoje, o GFRC é utilizado em mais de 100 países. É aplicado em todo o mundo para fabricar uma vasta gama de produtos pré-moldados para indústrias de construção e engenharia civil.
De que é formado o GFRC?
O Glass Fiber Reinforced Concrete é constituído por uma argamassa de cimento Portland, areia, fibra de vidro álcali resistente, e é misturado com uma proporção controlada de água. Entretanto, dependendo do projeto, podem ser adicionados aditivos químicos, minerais e pigmentos.
A quantidade de fibra de vidro da mistura deve levar em conta o método a ser utilizado na produção do material. Os métodos comumente utilizados são o de pré-mistura (premix) e o de projeção simultânea (spray-up).
Para o premix, a quantidade de fibras é limitada para não afetar a trabalhabilidade da mistura. Isso ocorre já que os componentes são misturados antes do lançamento no molde.
Em contrapartida, o método spray-up favorece o emprego de maior quantidade de fibras, pois o material entra em contato com a mistura no momento do lançamento, o que não influencia a trabalhabilidade.
As fibras usadas no método premix possuem comprimento de 12mm, enquanto que para o método spray-up, são utilizadas fibras com comprimento de 30mm a 35mm.
A quantidade de fibra de vidro álcali resistente é muito importante do ponto de vista da resistência do compósito GFRC. Isso porque as resistências obtidas historicamente com os processos de pré-mistura tendem a ser menores do que as obtidas pelo processo de projeção simultânea. Simplesmente por causa da taxa inferior de fibras utilizadas.
Sendo assim, quando o assunto é o GFRC, para cada projeto há uma dosagem específica de fibra de vidro, encontrada por meio de estudos por conta de diversas variáveis que influenciam no processo.
O que se pode afirmar é que o cimento é o componente mais utilizado na mistura, cabendo a ele aglomerar os materiais e dar resistência ao compósito. A água, como de praxe, deve ser limpa e isenta de matéria orgânica.
Quanto aos agregados, o método premix sugere o uso de areia com tamanho máximo de partícula de apenas 2,4mm. Para o método spray-up, o tamanho máximo de partícula é geralmente limitado a 1,2mm. A preferência é pelo uso de areia de origem sílica ou areias de mármore e granito, se for o caso.
Com relação aos demais compósitos, as adições minerais proporcionam redução do pH da matriz cimentícia, o que reduz a alcalinidade da mistura. Isso é importante para a vida útil do compósito, que apesar de utilizar fibras de vidro álcali resistente pode perder resistência no decorrer do tempo..
Já a adição de polímeros acrílicos à mistura do GFRC permite uma cura do concreto subsequente seca e redução das fissuras de superfície. A presença desse aditivo é solicitada por conta do alto teor de cimento e baixa relação água-cimento. Além desses, os pigmentos em pó podem ser usados somente para produzir GFRC colorido.
Quais as grandes vantagens da utilização do GFRC?
O GFRC tem a plasticidade como uma das qualidades mais marcantes. Essa plasticidade proporciona efeitos arquitetônicos de alto e baixo relevo que seriam impossíveis de serem obtidos com outros concretos. Isso possibilita moldar painéis de fachada exatamente de acordo com o projeto de arquitetura.
A capacidade do material para ser moldado em placas finas, com uma ampla variedade de formas e acabamentos da superfície, tem sido apreciada por um público cada vez maior de arquitetos e engenheiros em todo o mundo.
Se comparado à alvenaria convencional, o Glass Fiber Reinforced Concrete pode agregar beleza, qualidade e velocidade na instalação. Resultado da pré-fabricação em fábrica, o que permite projetar e executar o produto com maior controle de qualidade.
Além disso, os painéis pré-fabricados em GFRC podem conter isolantes térmicos e acústicos, conforme as condicionantes do projeto, o que favorece a questão da sustentabilidade. Além disso, também há benefícios relacionados à redução do desperdício de materiais e à quantidade de entulho em comparação à vedação convencional de alvenaria.
Outra grande vantagem do GFRC é a leveza em comparação ao concreto convencional. Essa leveza tem ajudado também nos significativos avanços para a utilização desses elementos pré-fabricados.
O Concreto Reforçado com Fibras de Vidro é um material ideal para a reabilitação de edifícios. Painéis leves e finos são fáceis de manusear, além de minimizar o peso imposto à estrutura existente. Em muitos casos, a intervenção é feita não só para melhorar a estética do edifício, mas também para melhorar as propriedades térmicas e acústicas.
E as vantagens não param por aí. Por serem leves e fáceis de transportar, além de oferecerem resistência, os painéis de GFRC são propícios para a área de construção modular.
Tais produtos podem ter a seção transversal relativamente reduzida, devido ao ganho de resistência à tração e à flexão que as fibras de vidro proporcionam. Esse ganho acarreta em redução de peso, facilitando o transporte, armazenamento e instalação.
Com relação ao acabamento, o GFRC oferece boa redução de custos, já que a face exterior de cada painel já sai da fábrica com o acabamento final. Além disso, esses painéis já poderão contar internamente com as tubulações das redes hidráulicas e elétricas previstas no projeto.
Ao contrário do que acontece na Europa, o GFRC ainda é pouco utilizado no Brasil. Aliás, alguns dos maiores estádios de futebol do velho continente já utilizaram esses painéis em reformas, visando a não alteração das estruturas. Dois exemplos clássicos são o Estádio Santiago Bernabéu, do Real Madrid, na Espanha, e o Estádio San Siro, em Milão, na Itália.
Para a Copa do Mundo da África do Sul, o Estádio Soccer City, em Johanesburgo, também contou com 30.000m² de GFRC, aproximadamente 40.000 painéis. O estádio tem 60 metros de altura e capacidade para 95.000 pessoas, e o projeto tornou-se referência mundial no assunto.
Outra referência em Concreto Reforçado com Fibras de Vidro é a Igreja Sagrada Família, em Barcelona, na Espanha. Ela está sendo recoberta com muitas peças feitas do material, visto que ele possibilita a moldagem de peças esbeltas de desenhos rebuscados, com alto e baixo relevos.
Caso você ainda tenha dúvidas sobre o GFRC e as vantagens desses painéis, ou caso queira nos ajudar com outros conhecimentos, compartilhe seus comentários. E continue seguindo nossas publicações para ficar ainda mais por dentro dos assuntos relacionados à construção civil.